
Technical Summary DBK-10
DESCRIPTION - Single reflex band pass enclosure project.
OBJECTIVE - Using optimum alignment calculated and agreed upon by both driver manufacture and this team - Determine and document
the gap between optimal max. output and driver failure.
OBJECTIVE - Using observations and prior documentation, increase the gap.
OBJECTIVE - Raise optimal max. output.
DRIVER MANUFACTURE - Stillwater Designs
MODEL NO. C10-4
QT .29
R 4 ohms
FS 31.5
IB RESPONSE 25hz to 2000 hz +/- 5 dB
EF @ 40 hz 92.8 dB
EF @ 200 hz 96.5 dB
OPTIMUM ALIGNMENT - Enclosure as described
NET VOLUME SEALED CHAMBER 1209 Cubic inches
NET VOLUME VENTED CHAMBER 1036.8 Cubic inches
PORT DIA 4.0"
PORT LENGTH 12.25"
MEASURED OUTPUT - 31 hz to 102 hz +/- 2dB
OPTIMAL MAX. OUTPUT (lake street chamber) 116 db measured @ 154 watts
RMS. Failure point 118.5 db @ 294 watts RMS. Failure type - mechanical.
Failure sine 25 cycles.
OBSERVATION - First of all it was difficult to repeat the test three
times for verification because the thiel smalls measured differently on
the three samples. We have determined that to accurately average the
figure for optimal max. output and the failure point, several additional
woofers will have to be destroyed. For this reason, we have selected to
keep the current figure above, and allow for a 20 % variance.
OBSERVATION - In determining the gap, 2.5 dB/140watts we must remember
this gap is applicable only to the frequency band of the measured
output. The gap changed on further tests as optimal alignment was
changed so as to reduce the bandwidth and increase output.
OBSERVATION - To raise the optimal max. output we found that the gap
must be narrowed rather than increased. Increasing the failure point is
also increasing the starting point of the gap or optimal max. output.
When the thermal limit is reached we have a new failure type which voids
the project.
OBSERVATION - failure point is the result of non linear travel of the
voice coil in the magnetic gap. We have found that the circuit
impedance changes during this condition causing reduced dampening by the
amplifier as well as uneven air movement across the coil creating hot
spots. The port position in the vented chamber was moved 13 times to
reduce the condition. All that happened is that the location of the hot
spots moved in accordance with the port location suggesting a direct
relationship between the two.
OBSERVATION - By eliminating the port tube and using the equivalent duct
area to achieve the same FB we saw a noticeable increase in the optimal
max. output and failure point. This we conclude is due to the more
evenly distributed air pressures on the cone surface reducing the
twisting and rocking condition prior to the failure point.
OBSERVATION - Several duct designs have been tested. The improvements
are coming harder and harder now, however we have succeeded in reversing
the failure type. We now have thermal failure with little evidence of
mechanical damage. Our new adjusted gap is 3.3 dB/84 watts. The
optimal max. output has been increased to 118.5 dB at 209 watts RMS.
OBSERVATION - Additional work has been done with the duct design. By
adjusting the bandwidth to 38hz to 250hz with a 9db hump at 74 cycles
the duct length was such that it could be exactly terminated at the
center point of the driver. By introducing an angle tangent to the
speaker cone on the leading edge of the duct, we were able to reduce
mach speed on the duct and improve linear travel of the voice coil.
OBSERVATION - By creating a reduction at the exit point of the duct
in the shape of a half circle we were able to incorporate the principles
of varovents and horn loaded enclosures by creating a rubber throat effect
on the FB, now allowing it to change based on frequency. The result of
this was now a wider bandwidth with only a 4dB hump. Rather than the
peek amplitude of the hump decreasing, the rest of the bandwidth shelved
up.
OBSERVATION - We have observed after trying drivers of various specs not
matching the design original that this duct design is offering similar
performance in different band locations, meaning while the response is
changing with different drivers the percentage of increase is not. All
alternate drivers experienced thermal failure rather than mechanical.
All alternate drivers showed an increase in max. optimal output and a
raised failure point. Several of the lower power drivers demonstrated
over double their rated power handling.
OBSERVATION - It would seem as an unexpected result of this project that
we have more blown woofers laying around than we know what to do with,
and an enclosure that gives acceptable results with almost any woofer
designed for sealed enclosures. The reference box from Rockford
containing two RFP12's exhibited no better performance than half of the
alternate 10" single alignments tested. The original C-10 driver
outperformed the reference RFP box by 2.5db at any given output level in
the frequency band between 40 and 80 cycles.
MEASURED DATA
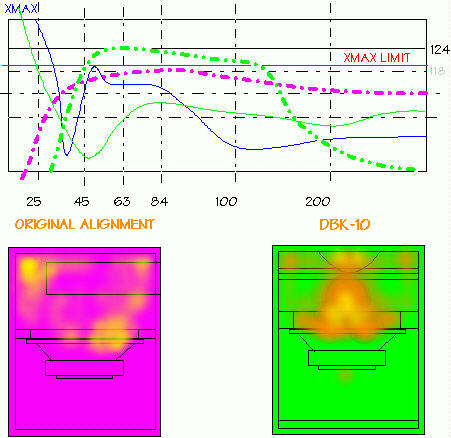
In the illustration above you can see the original optimal alignment &
its response. Notice the power handling indicated by the blue XMAX line
for this alignment. In the DBK-10 due to the improved duct design, the
power handling is greatly increased as illustrated by the green XMAX line.
Considerations were also incorporated into the duct design to effectively
couple with both large areas and smaller spaces like those found in car
audio applications. The new alignment while slightly higher bandwidth in
larger areas than the original alignment, offers good response in the lower
octave when cabin gains are calculated.
All field tests have confirmed
good or excellent flexibility in application.
|
HOME
BACK
Decware is a trademark of High Fidelity Engineering
Co. Copyright © 1996 1997 1998 1999 2000 2001 2002 2003 2004 2005 2006
2007 2008 by Steve Deckert
|